
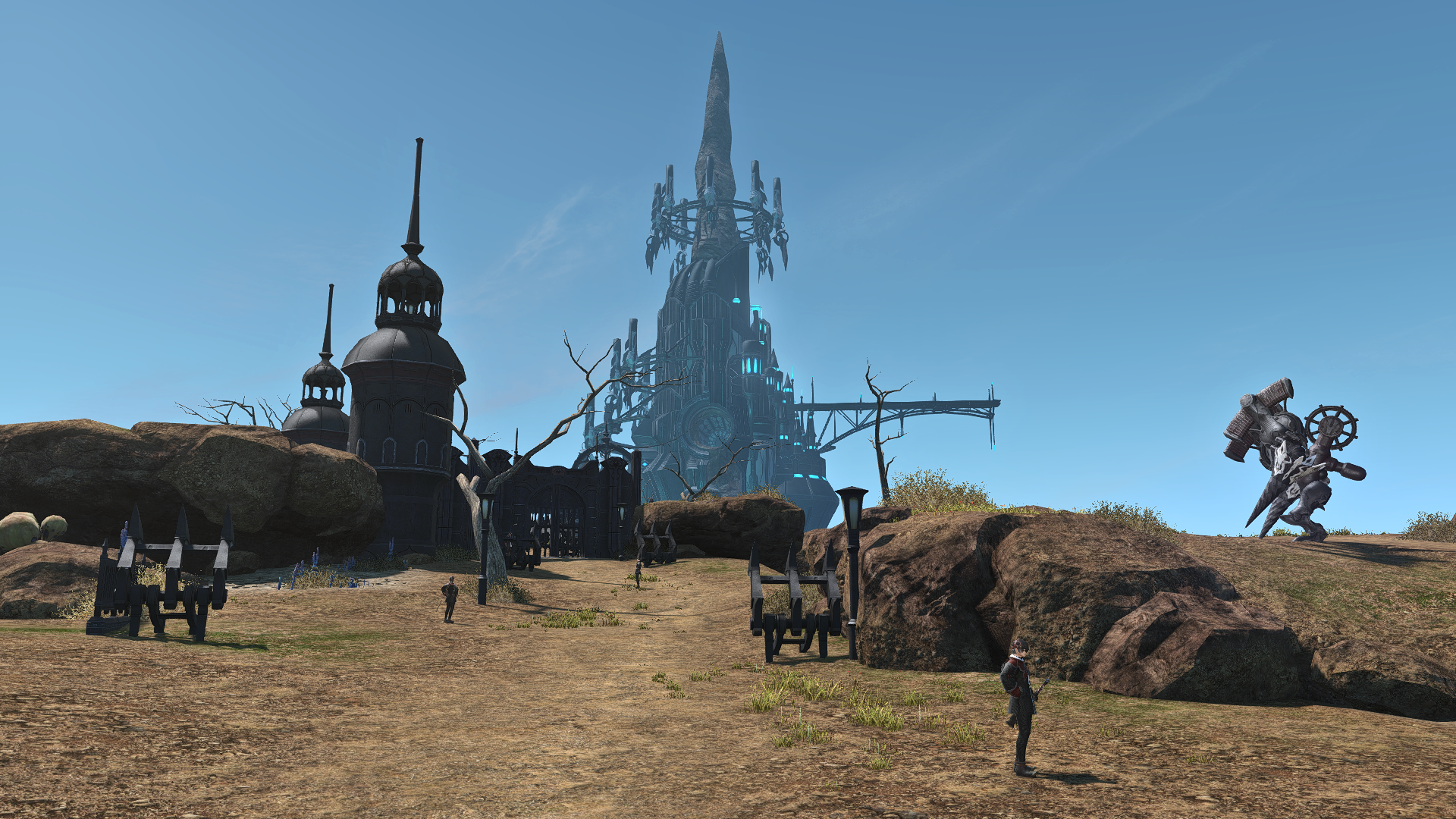
Chalcopyrite concentrate, dried and screened to remove large lumps, along with silica flux, is fed by screw from a hopper into the concentrate feeder (fig. Figure 3 shows the positions in the roof where the various products are introduced into the furnace and where the gas exits. Gases from the inner furnace pass out another water-cooled flue, through the roof, and also into a water scrubber. These gases discharge through a water-cooled flue into a water scrubber. A long flame from a hydrocarbon burner passes hot gases around the outer furnace. The outer furnace serves as a thermal barrier. The ratio of heat loss to input is inherently large in a small furnace and since it is desirable to maintain an atmosphere undiluted by outside contaminants, with only the products of reaction present, a double furnace was designed, as shown in figures 1 and 2. Oxygen is introduced by means of a water-cooled probe immersed into the matte bath where conversion to blister copper proceeds. The matte flows down an inclined crucible, countercurrent to the slag flow, to the converting zone at one end of the furnace. In the autogenous system described by this report, sulfide concentrate and silica flux are blown into the furnace through a specially designed burner with oxygen and is flash smelted to about 50-percent copper matte. the converter oxygen is introduced below the surface of the matte by means of an immersed probe.a very high, over 80-percent-concentration (low-flue-volume) SO2 gas is produced and.It is a continuous process utilizing commercial oxygen to produce blister copper in a single unit.The process described in this report, continuous oxygen smelting (COS), differs from the previously described processes principally as follows: slag is cleaned by passing through the low oxygen potential feed zone whereas reducing gas tuyeres are used in the Noranda furnace.copper flow is essentially continuous from a Weir, whereas in the Noranda system copper is tapped periodically after settling periods and.air or oxygen-enriched air is blown through the slag at high pressure to contact the matte bath for conversion to copper, whereas Noranda uses tuyeres.The slag flow is countercurrent whereas it is concurrent in the Noranda system.Worner, differs significantly from the Noranda process, as follows: metallic copper is tapped periodically after settling periods.continued injection of the gas into the resulting white metal oxidizes the Cu2S to metallic copper and.oxidizing gas is introduced into the matte to oxidize the FeS.matte and slag flows are controlled as they move slowly to tapping ports.Concentrates and flux are introduced in one end of the reactor which is similar in cross section to a Pierce-Smith converter.The Noranda process involves the following basic steps : Both use air or oxygen-enriched air and extraneous fuel to supply heat requirements. Two recent processes, Noranda and Worcra, utilize flash smelting and conversion to blister copper in a single unit. In both of these flash smelting processes, the matte is treated in converters. The latter is known as an autogenous (self-smelting) process since no extraneous fuel is used to smelt the remainder of the charge to matte and slag. The International Nickel Company’s flash smelting process at Sudbury, Ontario, utilizes commercial oxygen (95 percent O2) to produce a 45-percent copper matte and an SO2 gas consistently over 70 percent concentration. An SO2 gas concentration of about 13 percent is obtained. The heat from the reactions supplies a large part of the total heat requirements. In the Outokumpu flash smelting process developed at Outokumpu Oy in Finland, the furnace charge is blown into the furnace through a specially designed burner with air preheated to approximately 850° C. The offgases from the reverberatory furnace are usually not more than 2 percent SO2, and of varying SO2 content from the converters, precluding economic sulfur recovery in most cases.įlash Copper Smelting to matte has been a process improvement resulting in higher SO2 concentration. The predominant copper process is reverberatory furnace smelting of sulfide concentrates to produce matte and slag, followed by treatment of the matte in converters to form blister copper. Throughout this century the major production of copper (as it relates to Copper Smelting) and most other nonferrous metals has been through pyrometallurgical methods, treating sulfide ores by various batch processes. Slag Composition, Losses, and Forms of Copper.Test Procedure and Discussion of Results.Copper Smelting Furnace Construction and Refractories Used.Heat Balance Using Pure Oxygen Versus Air.
